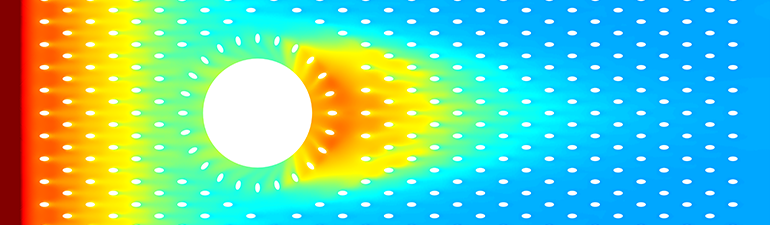
Conjugate Heat Transfer
Predictive Fluid-Solid Heat Transfer
In a simple world, you could simulate fluid flow and assume that the walls of the container were at a constant temperature or even adiabatic. In reality, however, the heat transfer between solids and surrounding fluids couples the temperature field in both materials, and thus your CFD software must be able to account for this phenomenon. CONVERGE features a state-of-the-art conjugate heat transfer (CHT) model for simultaneously predicting heat transfer in both the fluid and solid portions of the domain, which is critical for many applications.
Simulating Heat Transfer
Internal Combustion Engines
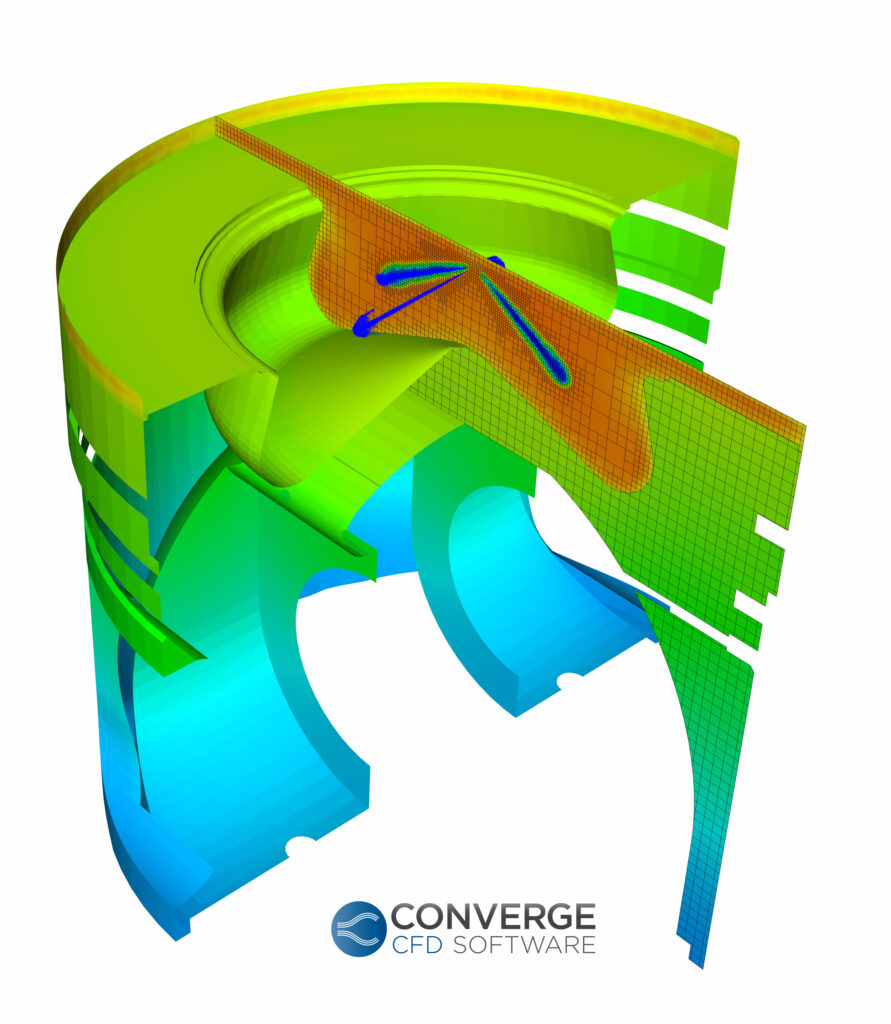
The internal combustion engine industry is moving toward simulating the entire system rather than independent components. The accuracy of the predicted combustion in the cylinder is dependent on the temperature boundary conditions in the cylinder. By considering heat transfer in the metal components (e.g., the cylinder head, liner, piston, etc.), the cylinder wall no longer has a user-specified temperature, but instead has temperatures predicted as part of the complete-system simulation. This makes the overall simulation results more predictive by reducing the dependence on assumed boundary conditions.
Electromobility
Effective cooling strategies are critical for various components of emobility systems. Electric motors have high power densities and thus generate a significant amount of heat. If a motor is not properly cooled, high temperatures in the motor can cause the demagnetization of the permanent magnets and the breakdown of the winding insulation. In CONVERGE, you can analyze a range of motor cooling methods using CHT modeling, including air cooling, water jacket cooling, and oil spray cooling.
For lithium-ion battery packs, CHT simulations are necessary for conducting cooling analyses under normal operating conditions and for predicting thermal runaway. Thermal runaway occurs when a cell reaches a temperature that triggers a cascade of exothermic reactions, causing the temperature to continue to increase. CONVERGE allows you to predict if a runaway cell will cause adjacent cells to initiate thermal runaway, which can be catastrophic to a battery pack.
Aftertreatment
Predicting and mitigating urea deposit formation is a key challenge in Urea/SCR aftertreatment systems. When urea-water solution is sprayed into the engine exhaust system, it impinges on the wall as a liquid film. The decomposition of urea and the formation of undesirable deposits are highly dependent on wall temperature, and the heat transfer between the film and the wall is important to capture. Predicting the wall temperature helps you identify areas that are vulnerable to wall deposition.
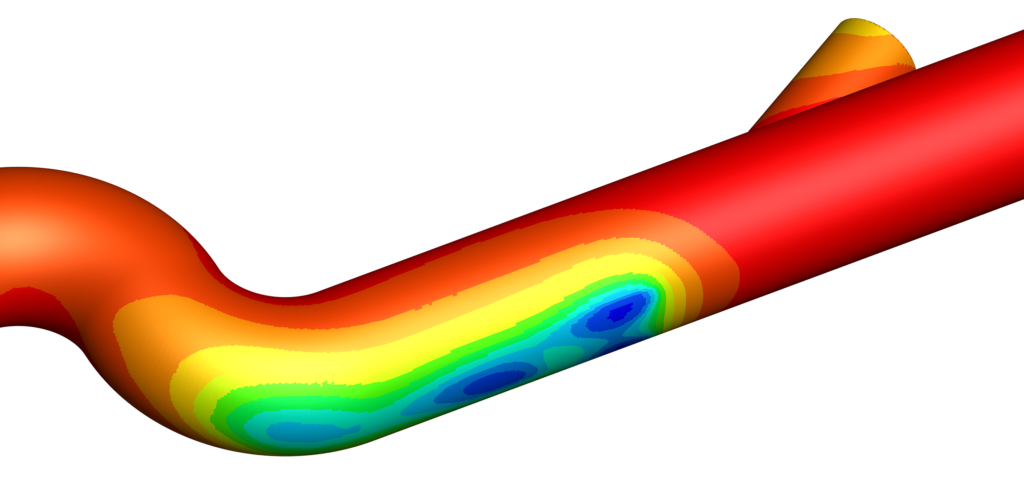
Aerospace
One way to achieve higher efficiency in gas turbine engines is to increase the temperatures inside the combustor. These temperatures often exceed the melting point of the metal alloys used to construct gas turbine combustors, necessitating methods for both cooling and insulating the combustor walls. With CONVERGE, you can accurately predict the combustor wall temperatures and analyze various cooling methods, such as effusion cooling, impingement cooling, and film cooling.
Liquid rockets are another application where capturing CHT is important. As the liquid oxidizer travels from the cryogenic tanks to the combustion chamber, it simultaneously cools the device and picks up heat along the way. The properties of the oxidizer depend on the temperature, often varying from a liquid-like supercritical fluid to a gas-like supercritical fluid, which significantly affects how the oxidizer will mix upon injection into the combustion chamber. Investigating the preheating of the liquid oxidizer is essential for accurately simulating combustion down the line.
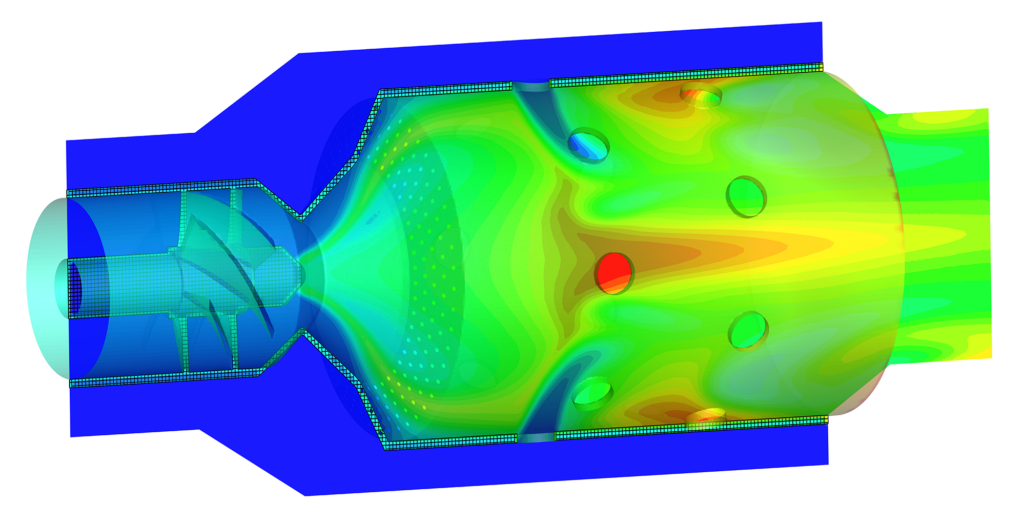
Pumps and Compressors
Resolving the spatially varying surface temperature distributions in pumps and compressors improves the accuracy of the simulation and provides useful temperature data. For example, in a twin screw compressor, thermal expansion affects the clearance between the rotors. If that effect is not captured, the simulations will incorrectly predict leakage flows and lower the accuracy of your results. By using CONVERGE’s CHT model to account for the rotor temperatures, you can then analyze the thermal expansion to accurately predict the gap sizes.
Accelerating CHT Calculations
There are several challenges when solving the fluid and solid domains together. The largest challenge to overcome is the difference in time-scales associated with the heat transfer in the fluid and the solid. In general, heat transfer in the solid occurs more slowly than the convective and diffusive time-scales of the fluid. This disparity in time-scales is problematic for CFD simulations because simulations of long physical time periods can be computationally expensive.
CONVERGE offers an alternative approach called super-cycling for overcoming the time-scale disparity. In super-cycling, the fluid solver is frozen periodically while the heat transfer in the solid is allowed to progress to steady-state. CONVERGE solves the fluid and solid phases in the same simulation without requiring you to stop and restart the simulation. Super-cycling significantly reduces the computational cost of the CHT simulation.
Another acceleration strategy in CONVERGE is the fixed flow method, which is useful for cases in which the flow changes less rapidly than other physical phenomena in your computational domain. By freezing the flow field and solving the flow for only short periods of time, the computational expense of the simulation is reduced. This is particularly beneficial for cases that require simulating a long period of physical time.